A2C supports its growth by constantly seeking sustainable alternatives, both in its supply chain and in the optimization of its processes.
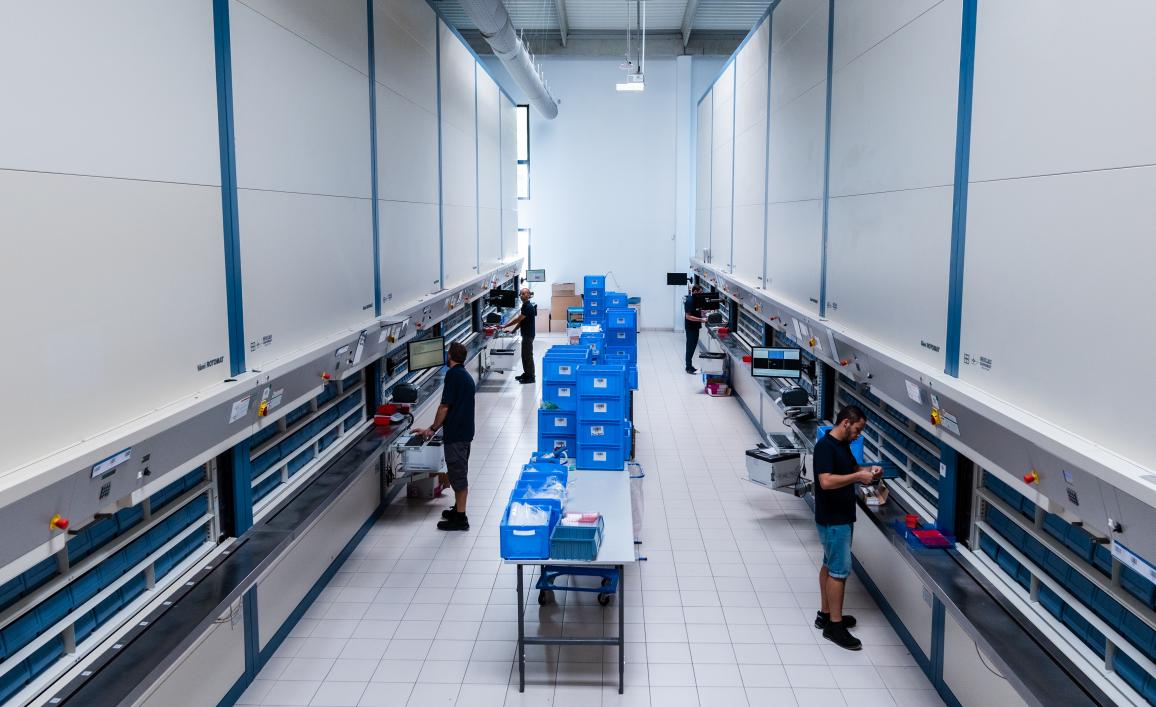
ORGANIZATION
Driven by the HEICO Group, A2C flourishes and benefits from this dynamic company's commitment to technological innovation.
Sharing our ambitions and best practices enables us, as a specialist in the distribution of electrical components, to anticipate the changes and constraints we face, and to organize ourselves accordingly. The management of product obsolescence and our proactive approach to environmental regulations are concrete examples of this.
A2C communicates its results, challenges and ambitions in full transparency with its stakeholders. Responsibilities within the company, our business strategy and our objectives are clearly defined and shared with all stakeholders and employees
APPROACH
A2C has been certified to EN9120 and ISO9001 standards for more than 15 years, to guarantee control of our processes and workflows.
A2C has also been certified by EN9100 and by our suppliers for the assembly of VAD connectors for several years.
As part of its environmental approach and the preservation of our natural resources, A2C's French site has been ISO 14001 certified for 10 years, proof of its mastery of its environmental impact.
The logistics and environment teams are constantly on the lookout for new, more responsible and sustainable packaging. Our processes are being digitalized to reduce paper consumption.
To go even further and improve its environmental footprint, the French site has embarked on the evaluation of its carbon emissions, on all its perimeters and throughout the value chain of its products.
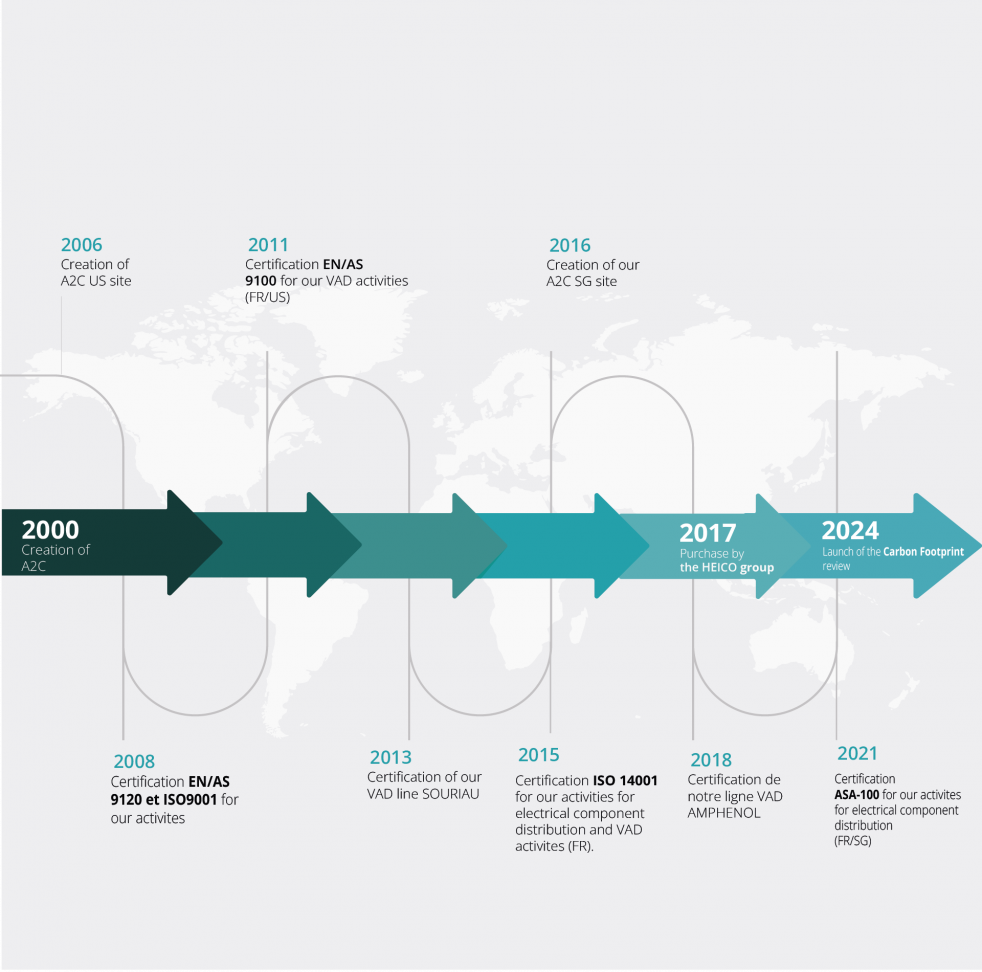
Within the limits of our technical constraints, we choose service providers who are recognized and certified for their eco-responsible sourcing approach.
At least 70% of the cardboard used to ship our products is recycled and 100% recyclable. Manufactured in Europe, they come from FSC-certified forests recognized for their responsible and sustainable management.
Recently, we equipped our shipping workstations with gummed tape to close our packages, made from corn pulp to limit the use of plastic products such as scotch tape while preserving the integrity of our products.
The digitalization of our processes and the pooling of our management systems between A2C entities enable us to challenge the quantity of paper used.
Wherever possible, we encourage re-use, and our teams are made aware of the importance of quality sorting to ensure the best possible recycling of our waste. For example, our printer cartridges, waste electrical and electronic equipment, coffee capsules and other special waste are all reprocessed in accordance with the applicable regulations.
EXPERTISE
To promote the development of our teams' skills and ensure continuity of service to our customers, A2C implements a robust training plan and encourages the versatility of our teams.
We capitalize on our experience and continuously improve our management system. Compliance with our processes is regularly assessed by means of controls and associated training for each of our employees.
Each new employee benefits from a training program adapted to his or her position, including a technical training course given by our experts to help them better understand the full range of products sold by A2C.
In the event of new training needs, each employee submits his or her request to the department in charge of follow-up, and we develop customized services in partnership with the Gers’ department organization.
Thanks to our experts in IT solutions, we are able to adapt our tools to our processes and constraints, while maintaining the efficiency of our operations.